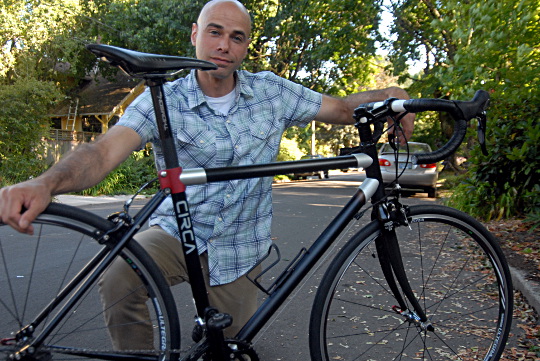
(Photos: M.Andersen/BikePortland)
A Portland startup is marrying the 1980s concept of “screwed and glued” modular frames with modern computer machining to dramatically cut the price of a custom handmade bike.
Its founder’s goal: a chain of minimalist, 600-square foot Apple Store-esque retail shops across the country, each one able to fit and service a line of Portland-built bikes as colorful and distinctly branded as iPods.
The man behind the plan is Rich Fox, a former innovation director at Nike and lead design strategist at Zeba Design. For the last 30 months, he’s been working from his basement to line up the components, branding and suppliers for a product that launched this morning on Crowdsupply, a Portland-based crowdfunding platform.
If there’s demand, Fox aims to open the first Circa retail shop in Portland next spring.
“Most of the bikes that are currently made here in the States, a bare frame will frequently cost $3000 and it will take anywhere from three months to five years to get that frame to you once you order it,” Fox said in an interview at his Northeast Portland home this month. “There are just very few people who can afford that kind of a product, in my opinion.”
So Fox says he’s broken down the major cost factors behind bike manufacture…
…and found a way to cut each of them, which he’s dubbed the “Mabel” process.
“I want to be Portland’s affordable handmade bike,” Fox said. “And in order to do that, I just had to really rethink the handmade process to make that happen.”
Advertisement
The process he’s developed, which uses CNC (computer-controlled milling) to shape the frame’s joints and adhesives to hold them in place, will deliver a 21.5-pound custom bike in the size and color combination of the owner’s choice in 10 days or less.
Circa’s frames sell for $1,100 and the completed bikes start at $1,500, with “town,” “city” and “road” versions that go up to $2,100.
The crucial tactic in Fox’s method, glue, is a tool he said the bike industry moved away from in the mid-1980s.
“Carbon started to come on the scene, and carbon was very sexy,” he said. “There were all sorts of fun swoopy doopy shapes you could do, so from a marketing standpoint everybody got distracted and wanted to see all the things you could do with carbon.”
But carbon-fiber frames are just too expensive for a very large market, Fox thinks. Glue and anodized aluminum are better and faster.
“We glue airplanes together; we glue race cars together,” Fox said. “So we can glue bikes together. Why the hell not?”
The distinctive three-color frame that has resulted is built for a designer’s eye: the joints are angled to create parallel lines and a sense of unity across the bike.
Fox’s first test ride of his prototype was during February’s snowstorm. He’s put 500 miles on it since.
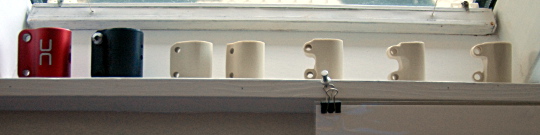
In order to guarantee his turnaround times and rapidly iterate his production process, Fox’s milling and piping suppliers are all in Portland. He intends that to remain part of the company’s identity and brand.
The bikemaking process is only part of Fox’s plan to shake up bike retail. He also wants to draw on ideas from Tesla and Apple to create a brand-specific bike shop.
“A typical bike shop is overwhelming from a sensory standpoint,” he said. “There’s too much to look at. There’s nowhere to rest your eye and there’s nowhere to rest at all in many of those joints. I’d like to have much more of a boutique experience.”
In Circa’s Portland shop, Fox says, the walls will be bare, but (he hopes) a glass wall will let people in the 600-square-foot retail space see into the larger manufacturing space behind.
If the Portland store is successful, his long-term goal would be to license franchise stores in cities like San Francisco, New York or Boulder, Colo.
Then again, he says, there’s also a chance that Circa’s crowdfunding campaign might show that people aren’t enthusiastic about the concept.
“If people look at this and say ‘That’s nice,’ and walk away, then I need to find another day job, you know?” he said lightly.
Thanks for reading.
BikePortland has served this community with independent community journalism since 2005. We rely on subscriptions from readers like you to survive. Your financial support is vital in keeping this valuable resource alive and well.
Please subscribe today to strengthen and expand our work.
Super. The look is a bit chunky / clunky but I’m sure they will find ways to refine it. I hope they succeed in a big way.
“chunky / clunky…”, how so? A detail shot showing how the lug ends make their transition to the tubing, may help to explain. In the picture at the top of the story, the frame’s joints don’t look particularly graceful, though maybe it’s possible to fairly easily change that.
In terms of style and looks, fatter tubes don’t seem a problem to me. For years, since steel was the only game going, there have been some very good looking frames with fat aluminum tubes, like those of Klein and Cannondale in earlier years. I think one of the things that make them look great is how the parts of the frame are finished to smoothly transition to each other.
Thanks, wsbob. We worked really hard on many of the precision details that don’t quite come out in the pics here. You can see them much more clearly on our site (www.ridecirca.com).
Intriguing idea. These days, $1100 is an excellent price for a custom frame, but just be clear most custom frames do NOT cost anywhere near $3000.
Neat looking bikes. I’m not clear on what’s custom about them, though, since they seem to come in just 3 sizes & 6 paint schemes. Being able to put different handlebars & derailleurs on it doesn’t make it ‘custom’, it just makes it a bike.
Hi Dan. The structure of a crowdfunding campaign makes it really difficult to offer true custom. Our goal is to offer full custom in generation 2 of the products, with custom geometry and colors.
Thanks for the clarification Rich. I was confused by the misleading caption on the first photo, which says “custom bike frames”. I like the lugs on the bikes.
Thanks, Dan! The MABEL™ manufacturing method will also give us the ability to have different shapes and styles for those lugs as we get the business up and running.
Why? Given it’s not being offered in true custom sizes, what possible advantage does this offer a consumer over a factory-made Trek/Giant/etc? It seems like a solution in search of a problem.
Hi Dave-
See my reply above to Dave.
http://bikeportland.org/2014/08/18/can-circa-cycles-bring-1500-custom-bicycles-mainstream-109955#comment-5385524
Yes, I saw that, but it doesn’t answer my question at all. Why would I buy this over a $1000 factory-made bike?
Not everyone wants a factory-made bike. Sometimes you have to pay a little more to have something interesting, new, innovative and/or unique.
Absolutely.
But this is a factory-made bike, no? The crowdsource page mentions three frame sizes, not “we can cnc any geometry you desire” — a stock bonded frame for $1100 is not any great deal when there are dozens of US framebuilders who can make you a fully custom frameset for only slightly more than that price, and dozens of bicycle companies that will sell you stock frames for much less than that price.
Hi David- The bikes are made by hand in Portland. For the crowdfunding campaign, we can’t do custom geometry. In the future, we will be able to do a very cost-effective full custom.
This bike has a distinct advantage if you are a US worker. It is made here by US workers. I feel it is important to support businesses that make things here – unless, of course, you are not a US worker. Buying US-made products is truly patriotic.
oops, I meant my reply to Dan.
If there is any market that can support “hipster bike social gathering place” bike shops it’s Portland.
It may just be enough to bring about the “Hipster-pocalypse” that many of a BikeSnobNYC bent would welcome.
UNLESS they offer free Wi-Fi, overpriced coffee and snacks.
I thought Velo Cult was already filling that niche?
I hope he does well and sells every bike he can make. I hope his boutique store idea is successful. Business successes and bicycle successes are good for us all.
Thanks! We just want to contribute to the local economy with beautiful, innovative bikes that can compete with ‘global’ products.
Have the CNC cut some simple graceful scroll work into the lugs. Retro-grouches like me love that sort of thing.
The MABEL™ manufacturing method will also give us the ability to have different shapes and styles for those lugs as we get the business up and running (including graceful scroll work). I’d also love to have guest designers do lugs and colors for us.
I feel a Chris King collaboration coming on!
Oh wait, you said “affordable”… 😉
It looks like the rear triangle can be opened up to allow belt drive installation. Is that true?
Good eyes! That was the plan! We wanted to allow a wide range of drivetrain options.
Good luck Rich. I don’t see enough future for this but I’m not a dreamer. If and a big If I were to buy a carbon frame I’d want tons of R&D in to it.
Am I missing something here? These are not carbon, and the cost of most carbon frames comes from R&D, tooling, and marketing. The R&D component is why a $2000 carbon frame tends to ride dramatically sweeter than a $300 frame from eBay.
Great to see all the hard work pay off with this important milestone. Best of luck Rich! We’re cheering for you and these cool bikes.
Love this concept of the custom fit modular frame that can be bonded together in short amount of time for minimal cost. Make sure you focus on the product and let the retail aspect come afterward.
Thanks, Jake. I’m a product guy. For me, I have to work extra hard on the retail (and sales) part!
Not to split hairs, but if it’s machined by computers can you really call it handmade?
My wife and I (well it’s her business so mostly her) are kind of going through this philosophical debate as well. She is a crafts person (hand made – she’s even reluctant to hire help because she wants to actually make each item) but the 3-D printers are awfully tempting, especially as the costs come down and the resolutions get better.
On a side note.
Epoxy resins have come along way since the 90’s, no one should really doubt the strength of a glued frame (many commercial buildings are held mostly together with glue – even here in PDX where we have very high code standards for earthquakes. As long as the glue is the right kind (which I’m sure you’ve got covered) and it’s applied and cured at the proper temperatures the glued joints will probably out live the rest of the Aluminium frame.
I suppose you’re a “hare”, so I understand your need to split ’em ; )
The CNC machines only make the lugs. In their defense, most of the time, the CNC machines are made by Haas in California, which we see as a healthy evolution of our manufacturing ecosystem. The frames are assembled by hand from these CNC’d components and hand-cut tubes.
Somebody taking an old idea and updating it. I hope it works out!
I also hope he can make them stiff and strong enough. I raced on a Vitus 979 back in the mid-80s and still have that bike and another one. If you’re blessed with a fast, smooth pedal stroke those bikes rode really well, but I’m 60 pounds heavier than I was back in my heyday so I don’t dare ride them today without a lot of care.
I don’t like carbon. The failure mode is very “unfriendly”. Aluminum is better in that regard. What I’d really like is bonded titanium. Welding Ti is difficult, requiring a lot of skill and shielding gas. Bonded Ti would make fabrication so much easier that it would no doubt bring the price of a frame way down. Hopefully Circa will consider that in the future.
My first race bike was a bonded Alan Sprint, which I purchased in 1984, and still ride today for fun. It’s a fantastic bike, and definitely played a role in inspiring the Trillium. With respect to titanium (and other tubing materials) our MABEL™ process is material agnostic, so yes, it’s an easy jump to other, (or even mixed) material frames. We went with aluminum for the Trillium because it allowed us to hit a price point that was accessible for a larger number of people, while still providing great performance.
Reynolds 853
Vitus 979 frames were flexible because the aluminum tubes were standard diameter (same as steel framed bikes of the day). Older Cannondales were stiff, because the aluminum tubes were oversize. If this bike uses oversize tubes, it can be as stiff as desired.
Stiff and strong doesn’t seem to be an issue with the first builds! It’s been incredibly stiff, but surprisingly comfortable due to the combination of tube choice and geometry.
Diameter is only part of the equation. Tubing thickness is the other part. Vitus could have made the tubes stronger by increasing thickness, but that sacrifices a lot of the weight savings. The Cannondales were stiff, all right. They rode like hell, too. Somewhere in the middle between Cannondale and the 979 would probably be best for most riders.
I’ve spent lots of time on one of the more beefy Cannondales (and an Alan which is similar to the 979) and agree wholeheartedly. We believe we’ve achieved a very nice balance of rigidity, comfort and performance with this build.
Hey, you talkin trash about Vitus there? JK – loved my Vituses (Vitii?) Now on #3, and they are getting hard to find. Nice soft ride, but not meant for the 225 lb. curb-hopping rider, for sure.
Anyway, neat idea, but they lose me with all the apple-speak. I’ll be sticking with my local bike shop.
No trash talk on the Vitus. As I’ve mentioned in other responses, I have a mid-’80’s Alan that I love, (but I’m also relatively light-weight). Out of curiosity, what ‘Apple-speak’ bothered you?
Who is riding these frames? How many are out in the wild right now?
We currently have the one prototype that you see in the photo. I’ve been the primary test-rider, with about 500 miles on it in a wide range of conditions (see 2nd video on our campaign page for nasty weather and hill demo). The purpose of our crowdfunding campaign is to raise funds for refinement and build more bikes, which leads to more riders.
So let me get this straight: you made 1 bike, rode it 500 miles over 5 months (~20mi/week) and now you’re selling betas to crowdfunders. I mean, I guess that works for SRAM (see:road hydro discs). I hope you have some decent liability insurance.
We won’t deliver bikes to customers until they’ve passed the appropriate safety standards tests, which will happen during upcoming refinement activities. Proceeds from the crowdfunding campaign will be used to refine our designs, complete testing, and set up production. All progress to date has been self-funded.
It was nice seeing you and your bike again at ADX for Lunch Wagon. It looks like your Crowd Supply launch is really picking up steam!
It warms my heart to see people try to make manufacturing work in the US through innovation and I think you might be on to something here. Cheers!
Thanks, David! Good to see you, too! Best of luck on your project.
Hello, Looks interesting. Reminds me of my old Giant Cadex mountain bike that lasted 15 years before I converted it to a single speed city bike and eventually sold it. It was one of those generation of glued bikes that got poo poo’d but I still see it around town from time to time.
Have you had any thoughts about developing a travel version of your frame? I seems like a compression fitting on the lug would allow for this without a heavy S&S coupler.
Good luck and cheers
Yes, that’s come up a few times! We might not get there until gen 2 or 3, but it’s in the sketchbooks!
I would be curious about actual strength test data comparing glued frames to welded frames. Just like carbon, if a glued head tube were to fail it would do so suddenly with very little warning. I probably wound not buy the frame unless some good testing had been done to help me rest assured that my teeth will stay where they are.
Agreed. We won’t deliver bikes to customers until they’ve passed the appropriate safety standards tests, which will happen during upcoming refinement activities.
Any concern that anodize will be sufficient to prevent long-term frame corrosion? It is standard to anodize and paint aluminum parts in the aerospace industry.
Anodizing is a fantastic way to protect aluminum. It hardens the surface significantly, improving scratch resistance, and when done correctly lasts for decades. I personally own an anodized aluminum Alan road bike that’s 32 years old, and the finish looks brand-new. Our ‘raw’ finished frame elements are also anodized clear to get the protective benefits.
If you’d like to see a Trillium in person, I’ll be at Woonwinkel in Portland, Sunday, August 24 from 2-4pm.
Woonwinkel address: 935 sw Washington, Portland, OR 97205